The Atlas Copco compressor technique is a well-known concept. It is used on many types of air compressors. The company is one of the leaders in this industry. Moreover, the techniques they use to create these compressors are very efficient.
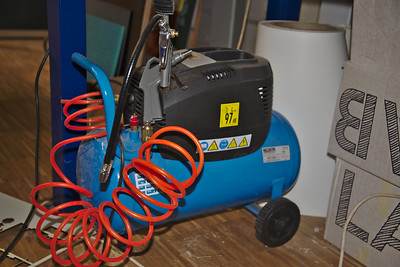
Centrifugal compressors
Atlas Copco is a leading manufacturer of an expansive range of products, including their renowned Atlas Copco compressor. Their compressors are designed for a variety of applications and high efficiency. These products are suitable for industries such as petroleum, power generation, and chemical manufacturing.
The company also has an extensive range of air filtration solutions, oil filters, separators, lubricants, service kits, and more. This equipment can be used to improve the performance of an existing compressor.
Atlas Copco is committed to delivering high-quality, reliable compressors to customers across the globe. From its beginnings in 1873, the company has developed a strong tradition of innovation. It is currently present in over 150 countries.
Atlas Copco provides a complete line of centrifugal compressors, which are designed to deliver a large supply of compressed air at a stable pressure. This makes the compressors very effective in industrial operations. Depending on the application, these compressors are available with a wide variety of impeller designs.
Vacuum technology
Atlas Copco has launched a new business area dedicated to vacuum technology. The group’s executives say they hope to become a global leader in this market sector.
This division will encompass a number of different product lines. It includes industrial and scientific vacuum solutions. In addition, it will also include a variety of products that are used in the semiconductor industry.
Vacuum solutions are used in many different industries and applications. These include pharmaceuticals, food packaging, chemical process industries, and semiconductor manufacturing. As a result, the company’s customers are located all over the world.
Edwards is a leading provider of sophisticated vacuum and exhaust management systems. They have state-of-the-art manufacturing facilities in North America and Europe. Their products are used in a wide range of R&D and industrial processes.
Leybold is a company specialising in vacuum and abatement technologies. They provide systems for a variety of applications, including semiconductor and flat panel display manufacturing. A key element of their technology is the integration of both vacuum and exhaust management technologies to ensure regulatory emission controls are met.
The new nitrogen generator
Atlas Copco has launched a new nitrogen generator technique. It combines two methods to produce ultra dry nitrogen. The technology uses pressure swing adsorption and membrane technology.
Membrane technology consists of a series of hollow fibres. The fibres have a circular cross-section. As the air is pushed through the fibres, the oxygen and nitrogen molecules adhere to the carbon molecular sieve. This separation allows the larger nitrogen molecules to pass through while the smaller ones are retained within the fibre.
In addition, the system features an automatic start-up, stand-by mode, and sensors that adjust the purity. These innovations improve performance and reliability while also reducing the environmental impact of nitrogen production.
Compared to high purity systems, the membrane technology has a lower initial investment and operational cost. Plus, it’s easy to install and modularly expand.
In addition, it provides a clean, dry source of nitrogen, which is practical in food preservation, plastic injection moulding, and fire prevention. Also, it can operate in high vibration environments.
FX dryers
Atlas Copco FX dryers are reliable and easy to use. They feature an effective control system that ensures a constant pressure dew point. These dryers are equipped with a digital display to monitor the machine’s performance.
Atlas Copco FX Series dryers provide maximum efficiency for your compressed air system. They are available in various sizes to suit your needs. In addition, they are a plug and play solution. The dryers require only a single electrical connection, and are pre-commissioned. This is a major advantage, as it allows for smooth start-up and operation. Besides, the dryers are quiet, and operate in full silence at all times.
Dryers are a vital part of your pneumatic equipment. They help remove moisture, which can cause rust and corrosion in your pipe work, and can lead to premature failure. It also helps to reduce the risk of condensation in your pipework. With a continuous supply of dry, conditioned air, you can eliminate this danger, and ensure that your products and tools stay in perfect condition.
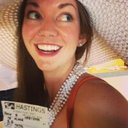
Krista Loeding specializes in travel and lifestyle content, exploring the intersection of elegance, comfort, and adventure in distinctive travel options.